Hot chamber Die Casting
Hot chamber die casting is a metal forming process ideal for creating parts from metals with relatively low melting points, typically below 450°C (842°F). Hot chamber isn’t ideal for metals with high melting points. The high heat could damage or corrode the integrated pot. Since the melting pot is integrated into the machine, there’s no need to transfer molten metal from a separate furnace. This eliminates a step in the process, leading to significantly faster production cycles compared to cold chamber die casting.
Hot Chamber Die Casting: A Speedy Process for Low-Melting-Point Metals
Hot chamber die casting is a metal forming process ideal for creating high volumes of parts from metals with low melting points (typically below 450°C). Here’s a step-by-step breakdown:
Melting: The process starts with the chosen metal, often zinc, magnesium, or other low melting point alloys, melting inside a pot integrated into the die-casting machine.
Injection: Once molten, a plunger mechanism forces the liquid metal through a narrow ” gooseneck ” channel that connects the pot directly to the die cavity. This injects the metal into the mold under pressure.
Solidification: The injected metal rapidly cools and solidifies within the die cavity, forming the mold.
Ejection: After solidification, the plunger retracts, and the machine opens. The solidified casting, now in its final form, is ejected from the die.
Repeat: The cycle then restarts with the plunger, injecting more molten metal into the die cavity for the next casting.
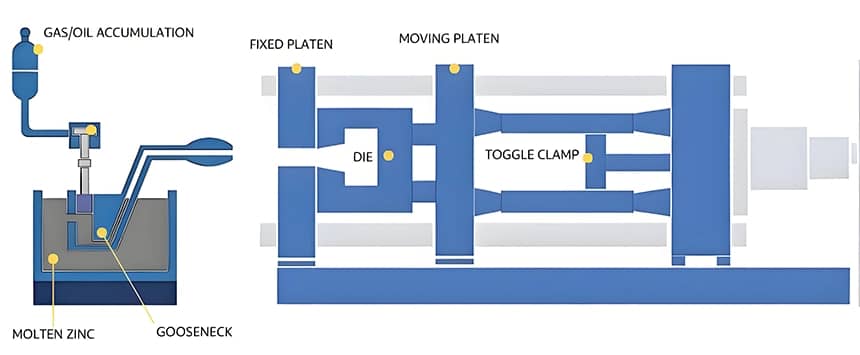
Advantages Specific to Hot Chamber Die Casting:
Faster Cycle Times: A hot chamber’s most significant advantage is its speed. The integrated melting pot eliminates the need to transfer molten metal from a separate furnace, significantly reducing cycle times compared to cold chamber die casting. This translates to higher production volumes.
Simple Operation: The integrated design makes operating the hot chamber less complex. Having both melting and injection within the same unit reduces equipment needs.
Cost-Effective: Due to its speed and simpler operation, a hot chamber can be a more cost-effective solution for high-volume production of parts from suitable metals (zinc, magnesium, etc.).
Considerations
Automated Processing: While modern die casting machines can be highly automated, it’s not unique to hot chamber and applies to cold chamber as well.
Waste Reduction: There can be some metal waste in the sprue (excess metal channel) during die casting, and hot chamber might not necessarily have a significant advantage here compared to cold chamber.
Design Efficiencies: Die casting design considerations can improve efficiency in both hot and cold chamber processes.
Die Casting Services: Your Partner in Precision Metal Parts
At DSW, we specialize in high-quality die casting services to meet your diverse metal part needs. Our experienced team offers a comprehensive range of capabilities, including:
Cold Chamber Die Casting: Ideal for high-strength metals like aluminum alloys, brass, and copper.
Hot Chamber Die Casting: Efficient for high-volume parts production from low melting point metals like zinc and magnesium.
Custom Die Mold Design & Development: Our engineers will collaborate with you to design and create the perfect mold for your unique application.
Diverse Material Selection: We offer a variety of metals to suit your project requirements best.
Why Choose DSW?
Precision and Quality: Our advanced die casting processes ensure exceptional part accuracy and repeatability.
Expertise and Experience: Our team has extensive knowledge in die casting to deliver optimal results.
Cost-Effective Solutions: We work closely with you to find the most cost-efficient approach for your project.
Ready to discuss your die casting project? Contact DSW industy today! We look forward to exceeding your expectations.
Start New Project Today …
Find the perfect supplier for your zinc alloy die casting needs.
No comment