Exploring Aluminium Alloys: Density and Applications
Aluminum is recognized for its lightweight, corrosion-resistant, and adaptable qualities, which make it indispensable in a variety of industries, including automotive, lighting, and aerospace. But why is aluminum so desirable in these applications? One important feature is the density of aluminum, which directly affects its performance, particularly in die casting. Aluminum has a density of 2.6 to 2.9 g/cm³, making it roughly one-third as dense as steel. This is a considerable advantage for weight reduction.
But the story doesn’t end with pure aluminum. Aluminum alloys, which combine aluminum with other metals, exhibit varying densities depending on their composition.
Why does density matter in die-casting?
The density of the alloy influences both the weight and the quality of the final product. Lower-density alloys cool faster, which can reduce porosity and improve surface finish. However, higher-density alloys—while offering increased strength—can lead to more shrinkage and casting defects. So, striking the right balance is crucial.
The relations between alloy composition and density influence almost every process element in various die castings, from mold design to material selection. Manufacturers must evaluate these elements to guarantee that the final parts meet the unique strength, durability, and weight requirements of industries such as automotive, lighting, machinery, and electronics.
What is Aluminium density?
Density quantifies mass per unit volume. Density (ρ) is mathematically defined as: Density (ρ) = Volume / MassFor aluminium, this refers to the mass of aluminium contained within a particular volume. Density quantifies mass per unit volume, an essential determinant of material behaviour under varying stresses.
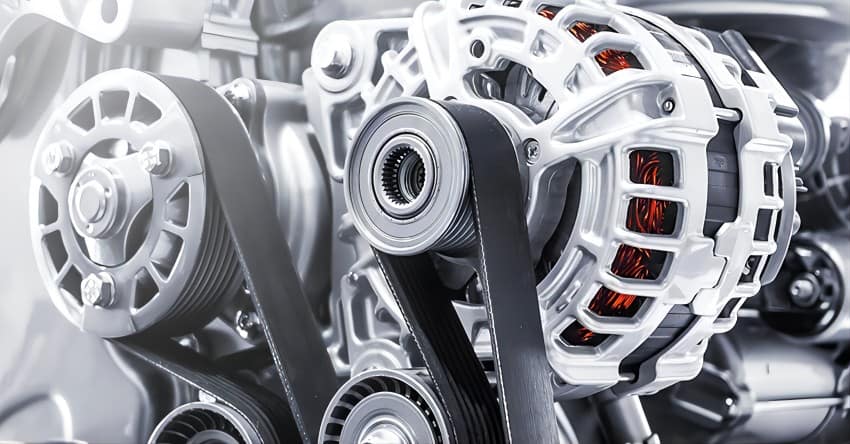
Density of Pure Aluminum
The density of pure aluminium is approximately 2,710 kg/m³ (0.1 lb/in³). The Aluminum Association standardises this value and serves as a benchmark for comparing the densities of aluminum alloys.
Density of Aluminium Alloys
The density of aluminum alloys typically ranges from 2,640 kg/m³ to 2,810 kg/m³. These variations are due to the small proportion of alloying elements added to pure aluminum. These alloying elements—such as copper, magnesium, silicon, zinc, and others—alter aluminum’s
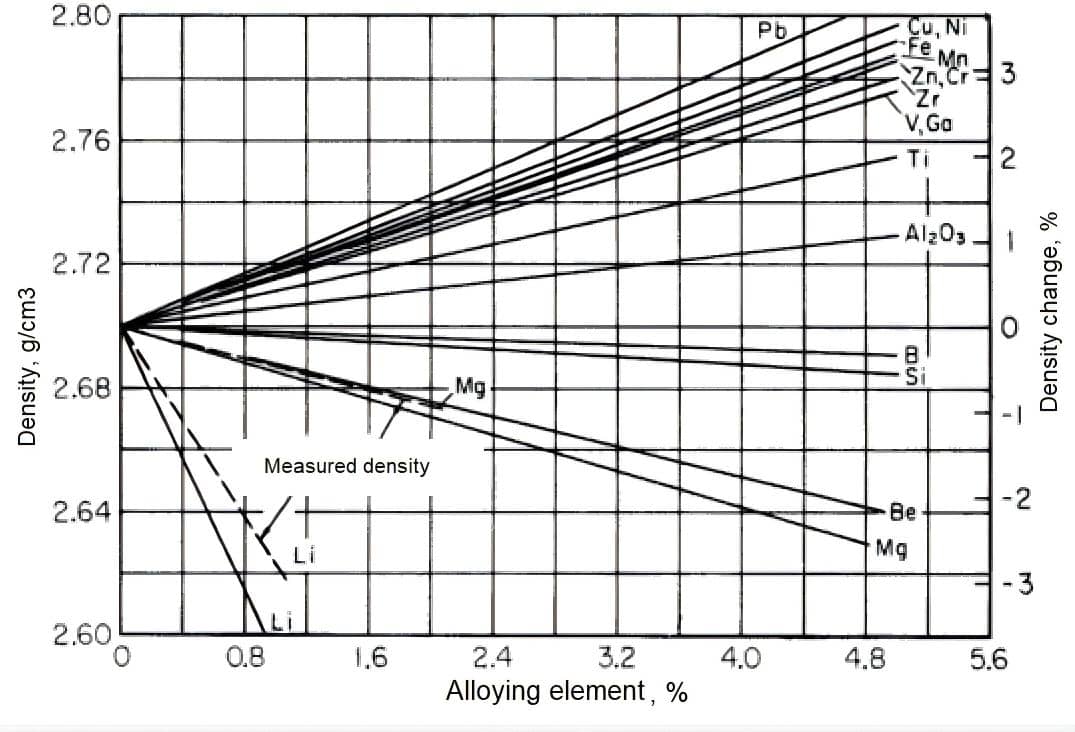
atomic structure and properties, impacting its density. For instance, the 5xxx and 6xxx series alloys are among the lightest because they primarily contain magnesium, which has a lower density.
Density of Aluminum Alloys: Effect of Alloying Elements
Adding alloying elements improves the qualities of aluminum—strength, corrosion resistance, heat resistance, and more. These elements also affect the density of the aluminum alloy, which is a basic factor taken into account for the material’s suitability for given applications. Together with their impacts on aluminum alloy density, the common alloying components are compiled here:
Alloying Element | Density (g/cm³) | Effect on Aluminum Density | Typical Applications |
---|---|---|---|
Magnesium (Mg) | 1.74 | Decreases density | Marine, automotive, lightweight applications |
Silicon (Si) | 2.33 | Minimal impact | Casting, automotive, structures |
Copper (Cu) | 8.96 | Increases density | Aerospace, structural components |
Zinc (Zn) | 7.14 | Increases density | High-strength applications, aerospace |
Manganese (Mn) | 7.47 | Slightly increases density | Beverage cans, automotive |
Lithium (Li) | 0.534 | Significantly decreases density | Aerospace, lightweight applications |
Iron (Fe) | 7.87 | Slightly increases density | Casting alloys |
Each alloying element brings a unique combination of properties that changes the density and strength, corrosion resistance, heat resistance, and other characteristics of aluminium alloys. These adjustments allow engineers to choose specific alloys tailored to the demands of their applications.
Density Chart for Aluminium Alloys
Different grades of aluminium alloys have specific densities:
Aluminium Alloy | Density (kg/m³) | Density (lb/in³) | Density (g/cm³) |
---|---|---|---|
1050/1060 | 2705 | 0.0977 | 2.710 |
1100 | 2710 | 0.0979 | 2.710 |
2011 | 2830 | 0.1022 | 2.830 |
3003 | 2730 | 0.0986 | 2.730 |
5052 | 2680 | 0.0968 | 2.680 |
6061 | 2700 | 0.0975 | 2.700 |
7075 | 2810 | 0.1015 | 2.810 |
Aluminium Densities in High-pressure Die Casting
In high-pressure die casting, aluminium density is a critical factor that influences casting quality, dimensional accuracy, and the component’s overall performance.
Aluminium Alloy | Density (kg/m³) | Density (lb/in³) | Density (g/cm³) |
---|---|---|---|
ADC12 (A383) | 2,740 | 0.099 | 2.74 |
A380 | 2,710 | 0.098 | 2.71 |
Alloy Densities in Low-Pressure Die Casting
Here’s a comparison table for aluminum alloy densities in low-pressure and gravity die casting.
Alloy | Density (g/cm³) | Key Properties | Typical Applications |
Aluminum (A356) | 2.6–2.8 | Lightweight, corrosion-resistant, good mechanical properties | Automotive, aerospace, general engineering |
Magnesium (AZ91D) | 1.7–1.8 | Extremely light, high strength-to-weight ratio, prone to porosity | Automotive, aerospace, portable devices |
Zinc (Zamak 3) | 6.6–7.0 | Excellent fluidity, good surface finish, strong but heavy | Electronics, automotive, decorative items |
Copper (Bronze/Brass) | 8.8–9.0 | Strong, wear-resistant, good electrical conductivity | Electrical components, industrial machinery |
The density of aluminum alloys varies across different casting methods, with low-pressure die casting (LPDC) generally producing the highest density and high-pressure die casting (HPDC) and gravity die casting (GDC) having slightly lower densities due to varying levels of porosity.
Relationship Between Aluminium Densities and Die Casting Design
The die-casting design depends much on the density of aluminum alloys. Optimizing the last product’s performance, efficiency, and cost-effectiveness depends on clearly understanding this link. The following key elements demonstrate how aluminum alloy density influences die-casting design:
Weight Considerations
Lower-density alloys produce lighter components, which are especially important in sectors like automotive and aerospace, where weight reduction is critical.
Lighter parts help to enhance fuel economy and lower emissions in automotive applications by themselves.
Strength-to-Weight Ratio
Aluminum alloys with an ideal strength-to-weight ratio help to create robust yet light constructions.
High strength-to-weight ratios are crucial in high-performance uses, including aerospace, where bulk reduction is vital.
Design Flexibility
Lower-density alloys provide design flexibility by enabling the casting of complicated shapes, such as thin-walled buildings and intricate forms.
Lower-density alloys help to increase the precision and usefulness of complex designs.
Thermal Conductivity
Excellent heat conductivity in aluminum alloys is highly sought after. Lower-density metals, particularly those used in electronic housing and heat sinks, help efficiently dissipate heat.
Automotive and aerospace uses depend on efficient heat management to guarantee the dependability of performance and safety.
Cost Efficiency
Lower-density alloys will help drastically cut material prices, lowering manufacturing costs.
Lighter components help reduce logistics expenses because they are more reasonably priced to move.
Mold Design and Lifespan
Alloy density directly influences mold wear and tear. Reduced wear from lower-density metals helps die-casting molds last for more years.
Cooling Rates: The density of the alloy influences its cooling rate, which in turn affects the design and efficiency of the mold’s cooling system.
Factors Influencing Density
Several elements and factors, including the following, influence the density of aluminum alloys:
- Alloying Elements: The general density depends on the type and ratio of alloying elements, such as magnesium, copper, and zinc.
- Processing: Grain size alteration, cold working, and heat treatment are some methods that can change density.
- Porosity:Porosity causes die casting alloys to have a density between 95% and 100% of their theoretical density.
Significance of Aluminium Density The low density of aluminium alloys offers several benefits:
- Lightweight: No aluminum alloy has a 3 g/cm³ density, so they are perfect for uses needing excellent strength-to-weight ratios.
- Selection: Due to their lightweight nature, aluminium alloys are favoured for structural frames, fluid dynamics, and packaging.
- Resistance: The oxide layer on aluminium alloys minimises exterior damage and corrosion.
- Reusability: Aluminium alloys consume less energy during recycling, making them cost-effective and environmentally friendly.
- Acoustics: Aluminium’s high sound speed makes it ideal for speaker diaphragms.
- Conductivity: Aluminium’s electrical conductivity is twice that of copper, making it suitable for power transmission lines.
- Expense: Lower density reduces transportation costs, making aluminium a cost-effective option.
What is the Aluminium Alloy Designation System?
The aluminium alloy designation system uses a four-digit numerical code to classify aluminium and its alloys. Here’s a simplified breakdown:
Wrought Aluminium Alloys:
- 1xxx Series: Al with 99.00% purity or higher.
- 2xxx Series: Al with copper.
- 3xxx Series: Al with manganese.
- 4xxx Series: Al with silicon.
- 5xxx Series: Al with magnesium.
- 6xxx Series: Al with magnesium and silicon.
- 7xxx Series: Al with zinc.
- 8xxx Series: Al with other elements.
The last two digits identify the specific alloy or purity level. The second digit shows modifications or impurity limits.
Cast Aluminium Alloys:
- 2xx.x Series: Al with copper.
- 3xx.x Series: Al with silicon, copper, and/or magnesium.
- 4xx.x Series: Al with silicon.
- 5xx.x Series: Al with magnesium.
- 7xx.x Series: Al with zinc.
- 8xx.x Series: Al with tin.
- 9xx.x Series: Al with other elements.
The cast alloys’ extra digits and decimal points help specify the exact composition and form.
Unique Properties of Aluminum
Aluminum’s density contributes to several desirable properties, making it suitable for a wide range of applications:
- Lightweight: Aluminum’s low density makes it an ideal material for applications requiring light weight and high strength, such as aerospace and automotive industries.
- Corrosion Resistance: Aluminum forms a protective oxide layer that prevents corrosion, enhancing its durability.
- Recyclability: Aluminum is 100% recyclable, making it an environmentally friendly choice. Recycling aluminium requires only 5% of the energy needed to produce new aluminium.
- Electrical and Thermal Conductivity: Aluminum is an excellent conductor of heat and electricity, making it suitable for electrical transmission lines and heat exchangers.
Applications of Aluminum Alloys
Aluminium alloy is widely cast in various industries due to its lightweight strength, corrosion resistance, and excellent thermal and electrical conductivity. Here are some key applications:
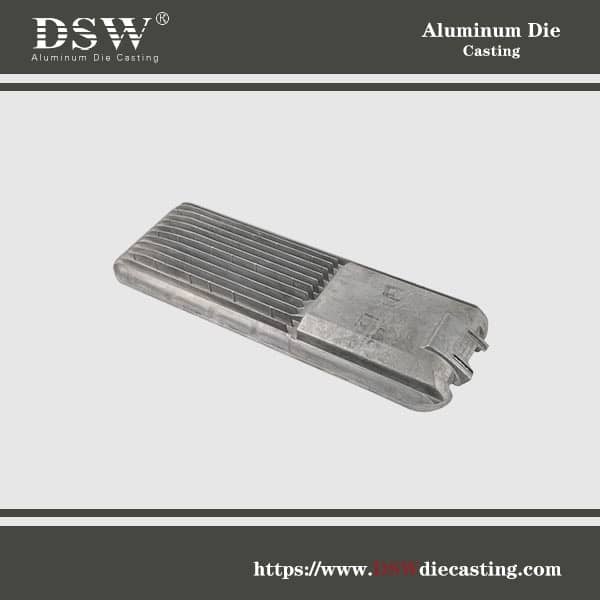
- LED and Outdoor Lighting: Aluminum die-cast components are often used in housings for LED and outdoor lamps, providing weather resistance, strength, and heat dissipation.
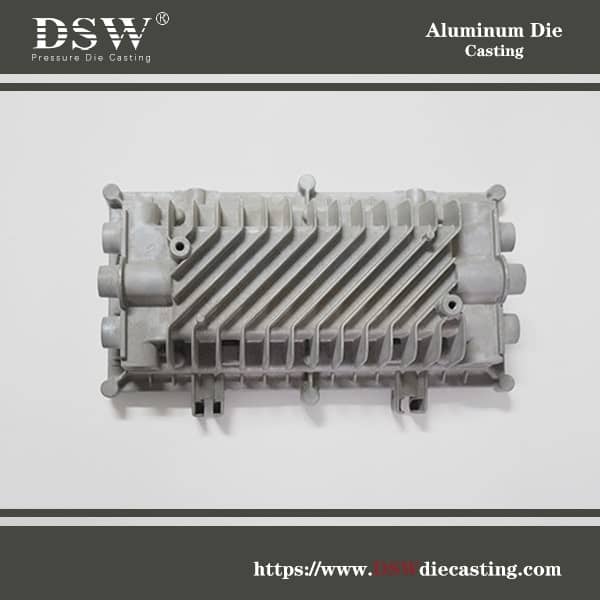
- Enclosures for Networking: Aluminum die-casting provides shielding and thermal management in protective casings for routers, modems, and communication devices.
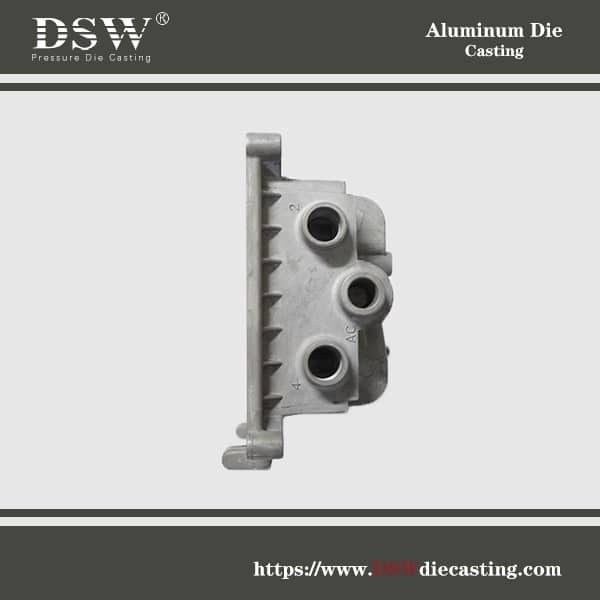
- Heat Sinks and Casings: Electronics such as LED lights, amplifiers, and CPUs use die-cast aluminum for heat dissipation and casing protection.
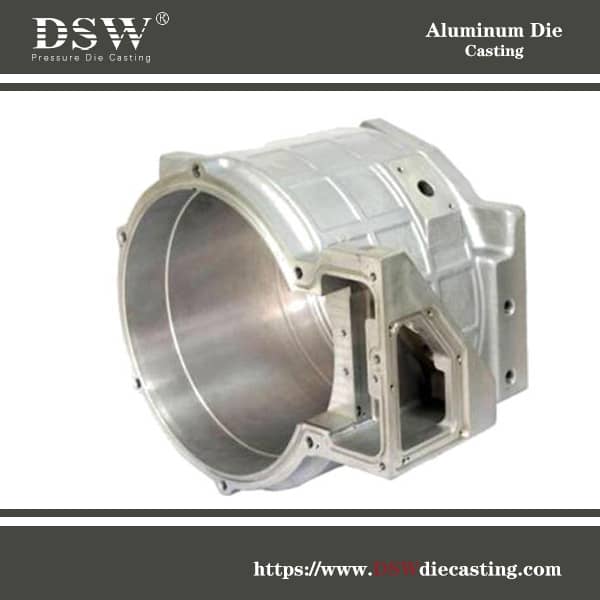
- Engine Components: Cylinder heads, engine blocks, transmission housings, and oil pans are made using aluminum alloy die casting for weight reduction and durability.
These additional applications demonstrate the versatility of aluminum alloy die casting in numerous fields. They enhance product design and performance while reducing costs and weight. In conclusion, selecting the right aluminum alloy for die casting is a delicate balance of factors like density, strength, and cooling behavior. Manufacturers must carefully consider these elements to optimize performance, cost, and sustainability in their applications.
No comment